Die Casting and Injection Moulding: A Comprehensive Guide to Metal Fabrication
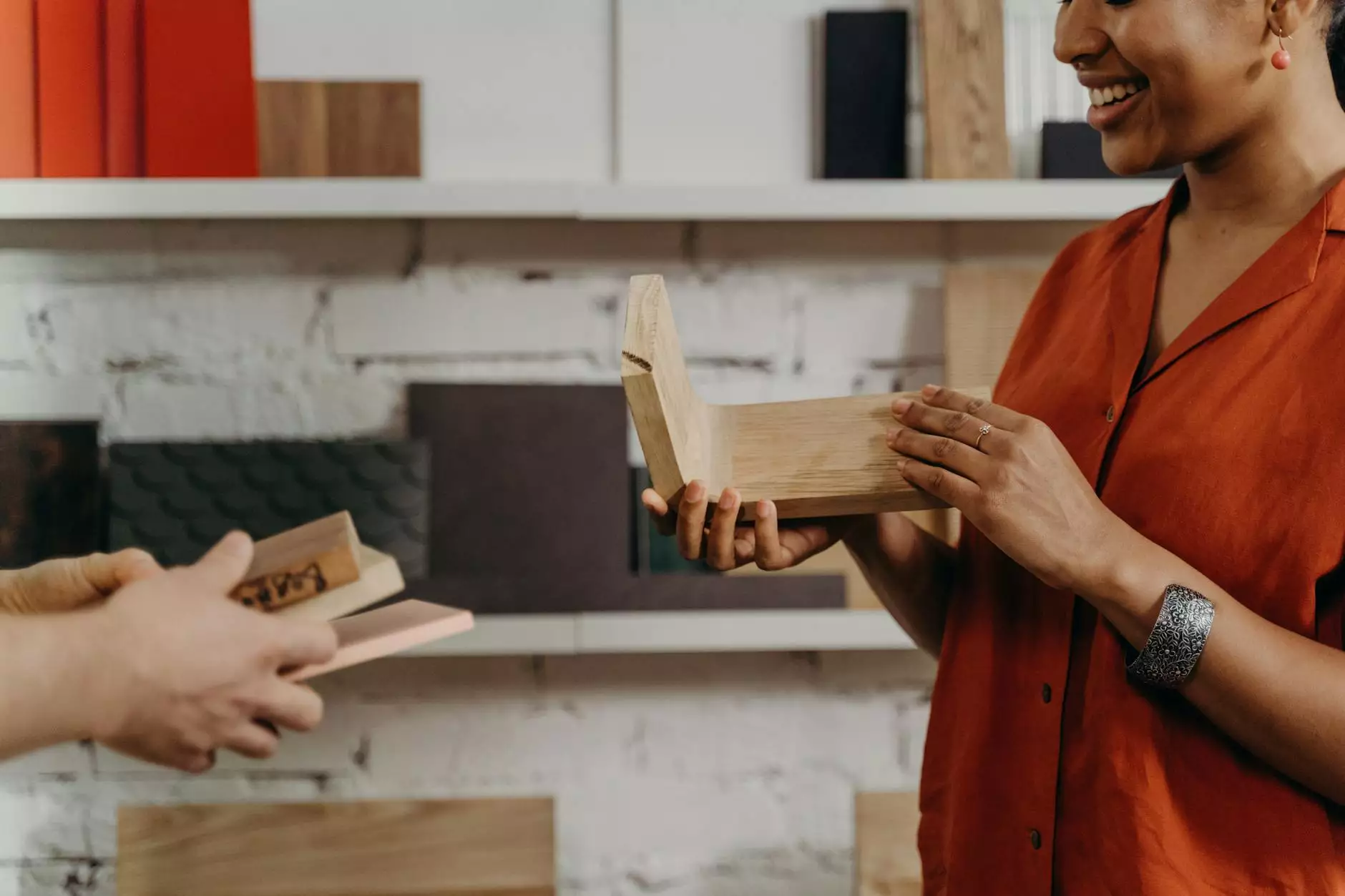
Die casting and injection moulding are two pivotal processes in the realm of metal fabrication and manufacturing, each serving unique purposes and yielding impressive results. In this article, we will delve deeply into these processes, exploring their methodologies, advantages, applications, and significance in the manufacturing industry. Understanding these processes not only aids manufacturers like deepmould.net but also empowers businesses to make informed decisions regarding their production techniques.
Understanding Die Casting
Die casting is a metal casting process that involves forcing molten metal under high pressure into a mould cavity. This method allows for the creation of complex shapes with high dimensional accuracy and smooth surfaces. Primarily, die casting employs non-ferrous metals such as aluminum, zinc, and magnesium due to their excellent fluidity and corrosion resistance.
The Die Casting Process Explained
The die casting process consists of several essential steps:
- Preparation of Die: The die or mould is prepared, typically from steel or iron, which is durable and can withstand high pressure and temperature.
- Melting the Metal: The chosen metal alloy is melted in a furnace, reaching temperatures that allow it to flow easily.
- Injection Phase: The molten metal is injected into the die at high speeds under immense pressure, which helps minimize the occurrence of air pockets and enhances surface finish.
- Cooling: The metal cools and solidifies within the die, taking the desired shape and dimensions.
- Ejection: Once solidified, the die opens, and the newly formed part is ejected.
Advantages of Die Casting
Die casting offers numerous benefits that make it an attractive choice for manufacturers:
- High Precision: Parts produced through die casting boast exceptional dimensional accuracy, which is crucial for intricate designs.
- Smooth Surface Finish: The process yields a smooth surface that often requires little to no secondary finishing.
- Rapid Production: Die casting is conducive to high-volume production, significantly reducing manufacturing time and costs.
- Material Efficiency: The process is highly efficient in terms of material usage, with minimal waste generated during casting.
- Versatility: Die casting can accommodate a variety of materials and alloy compositions, permitting adaptability to various industries.
Exploring Injection Moulding
Injection moulding is another cornerstone of modern manufacturing, utilized predominantly for producing plastic parts. However, it has also been adapted for metal applications in some contexts. The basic principle involves injecting heated material into a mould cavity to create a desired shape. This method is favored for its ability to produce large quantities of identical parts with high efficiency.
The Injection Moulding Process Explained
The process of injection moulding can be broken down into the following steps:
- Material Selection: The first step involves selecting the appropriate plastic or metal material to be used in the moulding process.
- Heating and Injection: The material is heated in a barrel and then injected into the mould under high pressure.
- Cooling and Solidification: The injected material cools and solidifies within the mould, taking the shape of the cavity.
- Demoulding: Once cooled, the mould is opened, and the finished part is ejected.
Advantages of Injection Moulding
The advantages of injection moulding are significant, contributing to its widespread use in the manufacturing sector:
- High Efficiency: Injection moulding is suited for mass production, allowing manufacturers to produce thousands of identical parts quickly.
- Complex Geometries: The process permits the creation of highly complex shapes and detailed designs that are difficult to achieve with other methods.
- Reduced Waste: Similar to die casting, injection moulding is efficient and generates minimal waste, making it environmentally friendly.
- Material Versatility: A wide variety of materials can be used, including plastics, metals, and composites, providing flexibility based on project requirements.
- Consistent Quality: The automated nature of injection moulding ensures consistent quality across large production runs.
Applications in Various Industries
The applications of die casting and injection moulding are extensive and span numerous industries:
Automotive Industry
Both die casting and injection moulding are crucial in the automotive sector for manufacturing components like engine blocks, transmission cases, and dashboard panels. The ability to produce complex shapes with precision makes these methods invaluable for ensuring safety and functionality in vehicles.
Consumer Electronics
The electronics industry relies heavily on both processes for producing casings, connectors, and various internal components. The smooth finishes provided by die casting and plastic injection moulding are essential for aesthetic appeal and functionality.
Medical Equipment
In the medical field, precision and reliability are paramount. Die casting is often utilized for making surgical instruments, while injection moulding is employed to create housings for medical devices. These applications require stringent quality controls, which both methods facilitate effectively.
Aerospace Industry
In aerospace manufacturing, weight and material performance are critical. Die casting is used to produce lightweight, strong components like brackets and housings, ensuring that aircraft remain efficient and safe.
Future Trends in Die Casting and Injection Moulding
As technology advances, so too do the processes of die casting and injection moulding. Emerging trends reflect a shift towards increased automation and improved materials:
Emphasis on Automation
Automation in die casting and injection moulding processes leads to reduced labor costs, improved precision, and faster production times. Robotic systems are increasingly utilized for material handling, quality inspection, and even the actual injection process, enhancing efficiency and reliability.
Advancements in Materials
Research into new materials is ongoing, with advancements in alloys and polymer formulations leading to enhanced performance characteristics. For instance, the development of lightweight metals for die casting and high-performance plastics for injection moulding sets the stage for superior product capabilities.
Sustainable Practices
With growing awareness of environmental sustainability, there is a strong push towards eco-friendly practices in both die casting and injection moulding. Manufacturers are exploring biodegradable materials, recycling scrap products, and optimizing processes to reduce energy consumption.
Conclusion
In conclusion, die casting and injection moulding represent fundamental processes in the manufacturing sector that provide unparalleled advantages in precision, efficiency, and versatility. Their applications across various industries showcase their importance and utility, cementing their place in the future of manufacturing. As innovation continues to evolve within these processes, businesses like deepmould.net remain at the forefront, ready to embrace advancements that improve production and sustainability.