The Teflon Tube Fittings Factory: Unlocking the Future of Fluid Dynamics
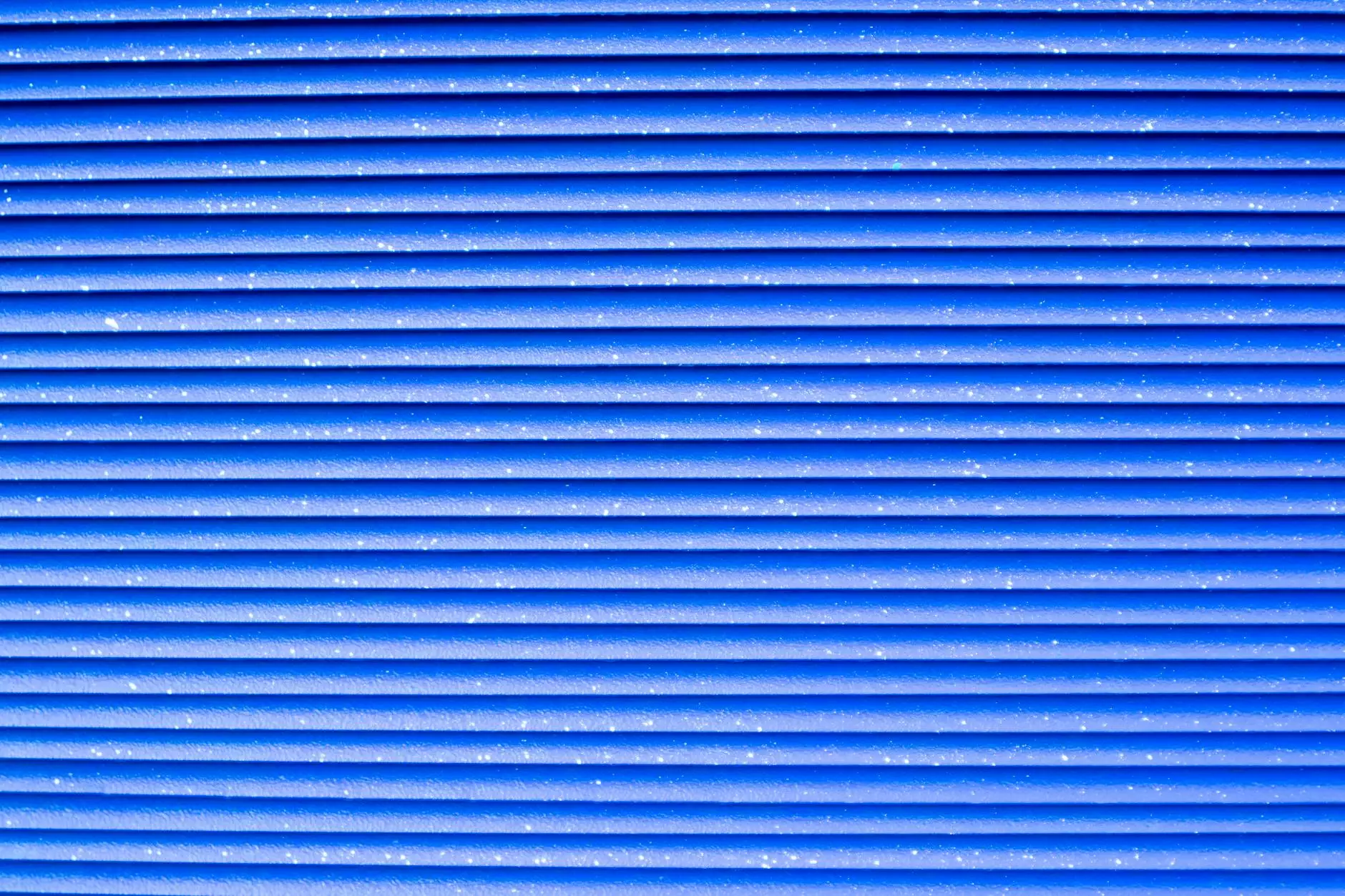
Teflon tube fittings have emerged as critical components across various industries, thanks to their exceptional resistance to corrosion, chemicals, and their ability to perform under high temperatures. This article delves deep into the significance of a teflon tube fittings factory, particularly focusing on its crucial roles, manufacturing processes, applications, and how businesses like Samvay Global have positioned themselves as key players in this market.
1. Understanding Teflon and Its Properties
The foundation of any discussion about Teflon tube fittings begins with understanding what Teflon is. Teflon, or polytetrafluoroethylene (PTFE), is a synthetic polymer known for its non-stick properties and resistance to heat and chemicals. Some of its defining properties include:
- Chemical Resistance: Teflon is nearly inert, making it ideal for applications where corrosive substances are involved.
- Heat Resistance: It can withstand temperatures of up to 260°C (500°F) without losing its integrity.
- Low Friction: Its surface has a low coefficient of friction, making it suitable for applications requiring smooth operation.
- Electrical Insulation: Teflon is an excellent electrical insulator, making it vital in a variety of electrical applications.
2. The Role of Teflon Tube Fittings in Various Industries
Teflon tube fittings are essential components used in a variety of industries, including:
- Pharmaceuticals: They are used in systems that handle harsh chemicals and sterile processes, where contamination is a concern.
- Food and Beverage: Teflon fittings help in the transportation of ingredients that require strict hygiene and temperature control.
- Aerospace: Their heat and chemical resistance make them suitable for aircraft systems.
- Oil and Gas: Used in transferring fluids safely and efficiently in challenging environments.
- Manufacturing: Vital in various manufacturing processes, ensuring minimal downtime and maximum efficiency.
3. Inside the Teflon Tube Fittings Factory
The manufacturing of Teflon tube fittings takes place in specialized factories, designed for precision engineering and high-quality production. Here’s a breakdown of the typical processes involved:
3.1 Material Selection
The first step in the manufacturing process is the selection of high-quality Teflon resin, ensuring that the final product meets industry standards and specifications. Factories often partner with reputable suppliers of Teflon resin to guarantee product quality.
3.2 Extrusion Process
In the extrusion phase, the Teflon resin is heated and forced through a die to create semi-finished products. This step is crucial as it determines the dimensional accuracy of the fittings. Innovative technologies are employed to ensure tight tolerances and uniform cross-sections.
3.3 Machining and Finishing
Once the extruded materials are cooled, they are cut and machined into the desired shapes and sizes. This stage involves:
- Turning: Using lathes to achieve precise shapes.
- Milling: Creating complex geometries as required by specific applications.
- Finishing: Applying surface treatments to enhance performance characteristics and aesthetics.
3.4 Quality Control
Quality control is a non-negotiable phase in a Teflon tube fittings factory. At this stage, products are tested for durability, dimensional accuracy, and chemical resistance. Adopting ISO standards ensures that products consistently meet required specifications and client expectations.
4. The Advantages of Choosing a Teflon Tube Fittings Factory
Engaging with a reputable Teflon tube fittings factory like Samvay Global offers numerous advantages:
- Expertise: A factory specializing in Teflon fittings has extensive knowledge and experience, leading to superior product quality.
- Customization: Many factories provide bespoke manufacturing options, allowing clients to tailor fittings to their specific needs.
- Cost-Effectiveness: Direct engagement with manufacturers often leads to lower prices compared to purchasing through intermediaries.
- Reliable Supply: Factories can provide consistent and reliable manufacturing, ensuring that supply chain demands are met.
5. Applications of Teflon Tube Fittings
The versatility of Teflon tube fittings enables their use in numerous applications, detailed as follows:
5.1 Chemical Processing
In chemical processing plants, Teflon fittings are utilized for transporting aggressive chemicals. Their chemical resistance drastically reduces the risk of leaks and contaminations.
5.2 HVAC Systems
Heating, ventilation, and air conditioning (HVAC) systems benefit from Teflon tube fittings due to their ability to withstand extreme temperatures and pressures.
5.3 Laboratory Equipment
In laboratories, where precise measurement and contamination prevention are critical, Teflon fittings are essential for connecting various components, ensuring clean and safe operations.
5.4 Automotive and Aerospace Industries
Both automotive and aerospace industries use Teflon fittings due to their lightweight yet durable nature, providing efficient performance in demanding conditions.
6. Future Trends in Teflon Tube Fitting Manufacturing
The future of Teflon tube fittings appears promising, with several trends shaping the industry:
6.1 Increased Automation
As technology advances, more factories are adopting automation to enhance production efficiency and product uniformity. Automated processes reduce human error and increase output rates.
6.2 Sustainable Manufacturing Practices
There is a growing emphasis on sustainability. Many factories are now focusing on reducing waste, recycling materials, and minimizing their carbon footprint in the production processes.
6.3 Advancements in Material Science
Research in material science may lead to the development of new Teflon composites, further enhancing the performance characteristics of tube fittings, such as improved flexibility or higher thermal stability.
7. Conclusion: The Value of Quality in Teflon Tube Fitting Manufacturing
In conclusion, the role of a teflon tube fittings factory cannot be underestimated in today’s industrial landscape. With its capacity to produce high-quality, durable, and reliable fittings, it serves as a backbone for various applications, ensuring safety and efficiency across different sectors. Companies like Samvay Global exemplify excellence in this field, offering leading-edge products and outstanding service. As industries evolve, staying ahead in manufacturing practices and embracing innovation will be key to maintaining a competitive edge.