The Future of Manufacturing: Harnessing the Power of Electric Injection
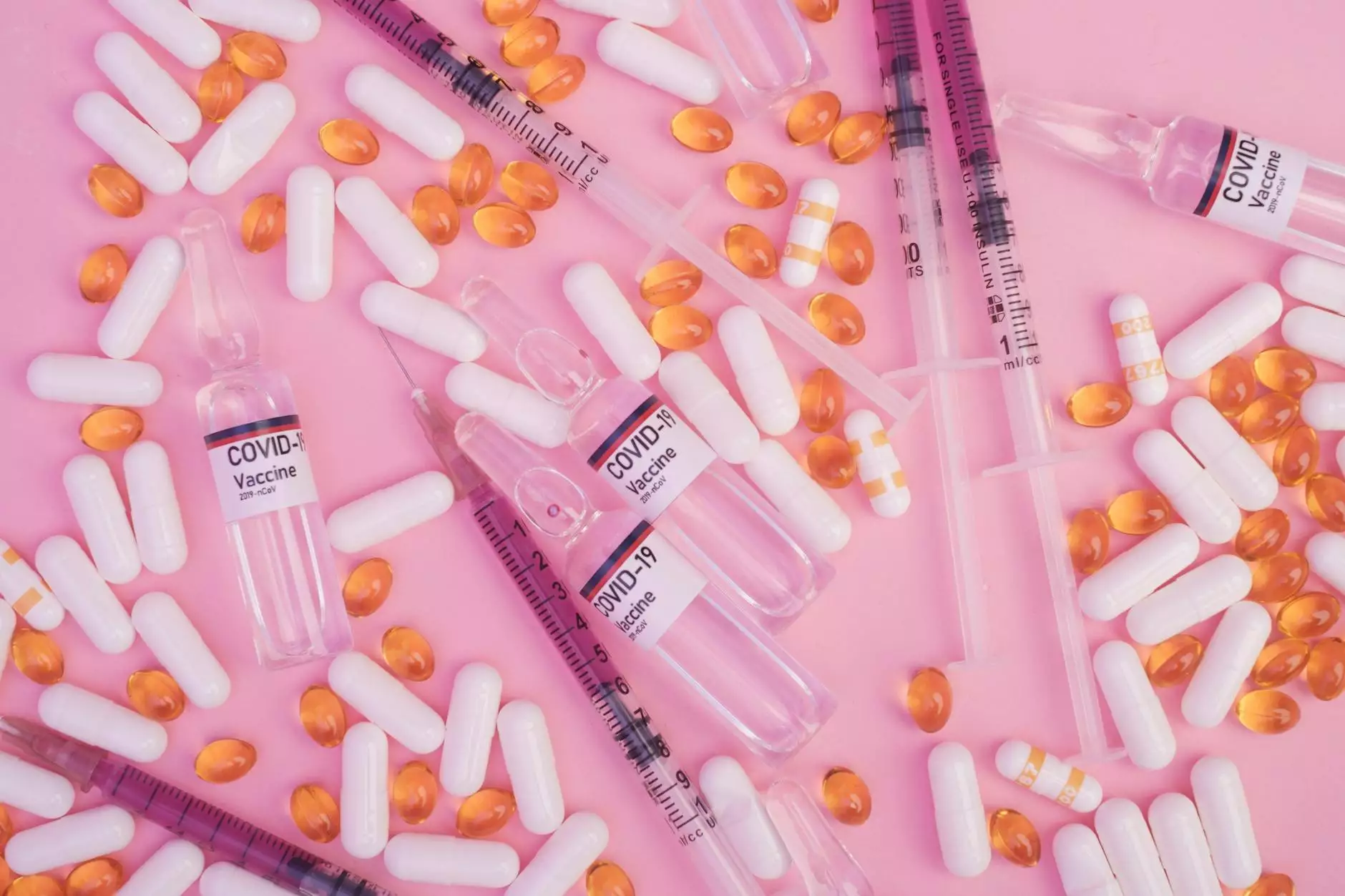
Understanding Electric Injection Technology
Electric injection is an advanced manufacturing process that transforms the way we approach metal fabrication and production. Unlike traditional methods that rely heavily on hydraulic systems, electric injection technology employs electric motors to drive the injection process, resulting in higher efficiency, better precision, and reduced energy consumption.
The Advantages of Electric Injection in Metal Fabrication
There are numerous advantages associated with using electric injection in the metal fabrication industry. Some of the most notable benefits include:
- Enhanced Precision: Electric injection systems provide superior control over the injection volume and timing, leading to more accurate and consistent results.
- Energy Efficiency: By utilizing electric motors, these systems drastically reduce energy consumption, making them more environmentally friendly and cost-effective.
- Lower Maintenance Costs: Electric systems generally require less maintenance than hydraulic systems, as they have fewer moving parts that can wear out or fail.
- Improved Cycle Times: Faster response times lead to shorter production cycles, increasing overall throughput and productivity in the manufacturing process.
- Reduced Noise Pollution: Electric injection systems operate more quietly than their hydraulic counterparts, contributing to a better workplace environment.
Applications of Electric Injection Technology
The versatility of electric injection technology allows it to be applied in various sectors within the metal fabrication industry. Here are some prominent applications:
- Aerospace: In the aerospace industry, precision is paramount, and electric injection proves invaluable for creating complex components that require meticulous specifications.
- Automotive: Electric injection technology is widely used in the automotive sector for producing parts that demand high strength and lightweight characteristics.
- Consumer Electronics: As devices become smaller and more intricate, electric injection plays a crucial role in manufacturing components that meet these specifications.
- Medical Devices: The strict regulations in the medical field require top-notch precision, where electric injection meets the industry's rigorous standards.
- Energy Sector: From solar panels to wind turbines, electric injection is employed in creating parts that contribute to sustainable energy solutions.
How Electric Injection Technology is Revolutionizing Metal Fabrication
The evolution of manufacturing processes has a direct impact on the efficiency and effectiveness of production lines. Electric injection is leading this revolution in several ways:
1. Process Optimization
With the incorporation of electric injection technology, manufacturers can optimize their processes to minimize waste and maximize quality. The precise control offered by electric systems also allows for real-time adjustments, improving the overall production rate.
2. Sustainability and Environmental Impact
As companies increasingly focus on sustainable practices, the shift to electric injection aligns perfectly with these goals. The reduced energy consumption and lower waste generation contribute not only to cost savings but also to a reduced carbon footprint.
3. Enhanced Product Quality
Electric injection ensures uniformity in production, which is critical for quality assurance. This consistency reduces the likelihood of defects and improves product lifespan, ultimately enhancing customer satisfaction.
Challenges and Considerations in Transitioning to Electric Injection
While the benefits of transitioning to electric injection are compelling, businesses must consider various challenges that may arise:
- Initial Investment: The upfront cost of electric injection machinery may be higher than traditional systems, which can deter some manufacturers from making the switch.
- Training and Skill Development: Employees may require training to operate new electric systems, which can take time and resources.
- Integration with Existing Systems: Existing production lines may need adjustments or overhauls to accommodate electric injection technology.
Future Trends in Electric Injection Technology
As technology continues to advance, the future of electric injection looks promising:
- Increased Automation: The integration of automation and electric injection will likely lead to smarter, more efficient production lines capable of self-adjusting based on real-time data.
- AI and Machine Learning: Incorporating AI into electric injection systems can enhance predictive maintenance and further optimize operational parameters.
- Customization and Personalization: Future electric injection systems may offer greater flexibility, allowing companies to produce highly customized parts with ease.
Conclusion: Embracing the Future of Manufacturing with Electric Injection
The transition to electric injection technology represents a significant step forward in the metal fabrication industry. By embracing this innovative process, businesses can enhance their production capabilities, improve product quality, and contribute to a more sustainable future.
As the industry evolves, staying informed about technological advancements will be crucial for companies looking to remain competitive. Investing in electric injection is not just about maintaining current market positions; it's about positioning for future growth and success.
If you're interested in learning more about how deepmould.net can assist your company in integrating electric injection technology into your metal fabrication processes, feel free to reach out to us. Together, we can build a more efficient and sustainable future for manufacturing.